L’entreprise Dracula Technologies a inauguré sa ligne de production de modules photovoltaïques organiques (OPV) le 12 septembre dernier à Valence. Avec une quarantaine d’employés, sept brevets déposés, un premier contrat commercial et des projets de développement ambitieux, l’entreprise applique le principe du « lab to fab » : une première étape de développement basée sur la recherche en laboratoire suivie d’un investissement dans un appareil industriel destiné à la mise en production de l’innovation.
La particularité des modules de Dracula Technologies ? Sensibles à la lumière naturelle et artificielle, ils fonctionnent à l’intérieur à partir de n’importe quelle source de lumière. Et c’est d’ailleurs en remplacement des piles que les modules de Dracula se pensent le mieux : dans les télécommandes, les petits objets connectés industriels, les capteurs ou mêmes pour alimenter les puces électroniques dans les centres industriels ou logistiques, le photovoltaïque français pourrait finalement creuser son sillon.
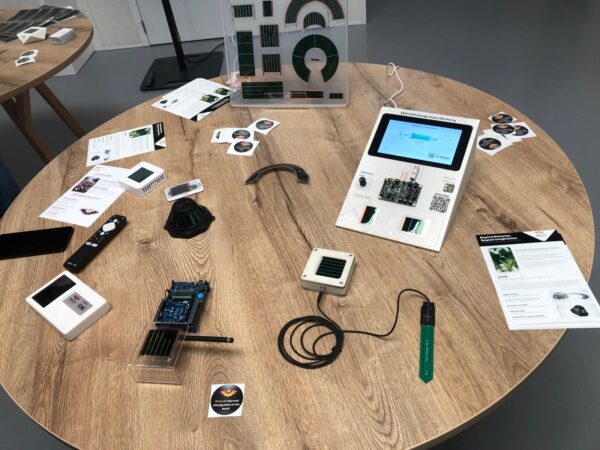
Image : MB
La «Green Micro Power Factory» présente aujourd’hui une capacité de production de 150 millions de cm² de surface active de modules photovoltaïques organiques. La production repose sur une technologie d’impression par jet d’encre développée par Dracula au cours de 12 années de recherche. Puisqu’ils sont imprimés, les modules peuvent prendre n’importe quelle forme sans sur-coût de production et s’adapter au besoin en puissance.
L’OPV : trouver la bonne formule technologique et industrielle
Le principe de la technologique OPV repose sur l’association d’un polymère semi-conducteur (donneur) avec un matériau organique (accepteur) qui constituent ensemble la couche active. Cette dernière absorbe puis transforme la lumière en énergie en créant des paires électron-trou liées (les excitons) qui se déplacent jusqu’à atteindre une interface donneur/accepteur (D/A) où a lieu la séparation des charges. Les porteurs de charge séparés se déplacent dans cette couche active jusqu’à traverser la couche photo-active, les couches interfaciales puis les électrodes pour atteindre le circuit externe.
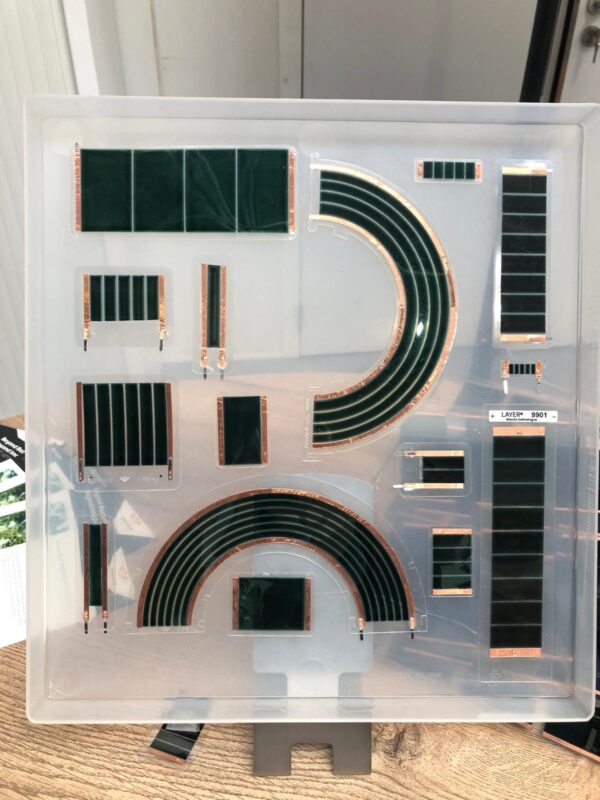
Image : MB
Dracula Technologies utilise le concept d’hétérojonction en volume où la couche active consiste en un mélange hétérogène de donneur et accepteur qui permet la mise en place d’une interface D/A très large. C’est d’ailleurs sur la composition et la nano-morphologie du mélange de couches actives (les encres) que l’entreprise marque sa valeur ajoutée et son secret industriel. Mais pas que, « nous travaillons également sur la compatibilité entre les couches », explique Sadok Ben Dkhil, le directeur de la technologie (CTO).
Dans la technologie OPV Layer développée l’entreprise, chacune des quatre couches est imprimée de manière à optimiser le transport des charges à la fois dans les matériaux et dans le module final. Dans l’usine de Valence, la salle blanche permet aux ingénieur⸱es et techniciens de produire ces différentes couches qui deviennent en quelque sorte les “encres” utilisées pour la production via l’impression jet d’encre.
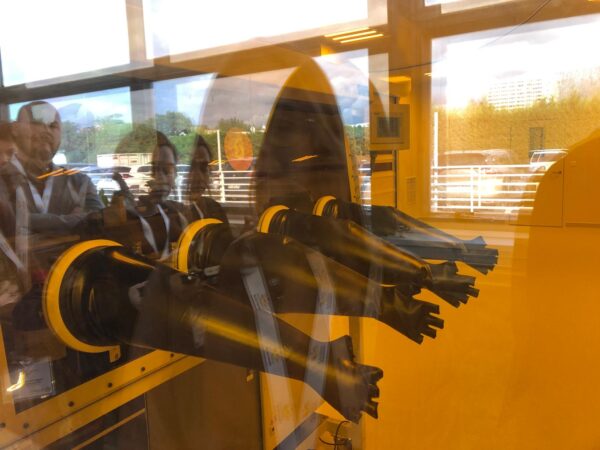
Image : MB
L’outil de production consiste donc en un écosystème intégré d’impression d’électronique. Une grande partie des équipements a d’ailleurs été racheté à son ancien partenaire de l’OPV, Asca, qui avait arrêté sa production un peu avant son rachat par l’Allemand Hering.
Dans l’usine de Dracula, les modules validés dans le laboratoire R&D sont transférés sur la ligne pilote afin de les optimiser. Ils passent ensuite en production automatisée : les cassettes de substrats accueillant le design du module sont placées sur l’îlot automatisé où ils sont pris en main par le robot qui les placent successivement vers les machines d’impression pour recevoir la couche d’encre correspondante. L’usine imprime une encre par jour, ce qui lui permet de gagner en efficacité. En effet, la couche active a besoin de temps pour se stabiliser et chaque impression doit être suivie d’un temps de repos pour laisser le temps aux résidus de solvants de s’évaporer. Les têtes d’impression sont munies de buses de quelques micromètres de diamètre qui permettent de projeter de manière uniforme des gouttelettes d’encre en créant des motifs précis. La maintenance de ces outils sensibles est au coeur de l’appareil industriel de l’entreprise.
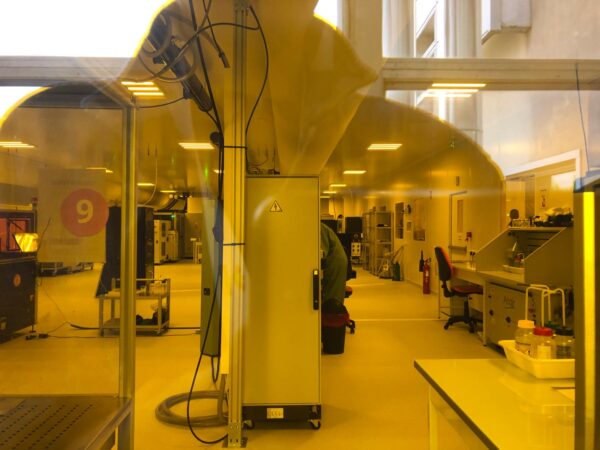
Image : MB
Car qui dit nano-électronique, dit (idéalement) zéro défaut. Et c’est le cas en dehors de la machine d’impression également. « L’automatisation nous permet d’éviter les défauts liés à la manipulation. Ils sont parfois imperceptibles à l’oeil nu lors de la production, mais à notre échelle de travail ils peuvent avoir une forte influence sur le résultat esthétique et technique du module final, explique Brice Cruchon, PDG de Dracula Technologies. Notre objectif est de passer à l’automatisation sur toutes les étapes de la ligne de production d’ici fin 2026 en intégrant des innovations dans notre process actuel ».
Un autre objectif pour la jeune usine est de multiplier par quatre sa capacité de production pour atteindre les 600 millions de cm² de modules d’ici 2026. Pour ce faire, Dracula envisage par exemple d’augmenter le nombre de “shift“, soit avec plusieurs équipes (du matin et du soir, voire les 3/8 en période de grosse production) soit en ouvrant la production sur les weekend. Elle entend aussi ouvrir de nouvelles lignes de production. Et ce n’est pas la place qui manque ! L’entreprise s’est installée dans des locaux industriels de 2500 mètres carrés. Mêmes les anciennes serres environnantes pourront être transformées en nouvelles salles blanches pour la suite du développement de la production.
Trouver le bon marché : remplacer les piles, mais pas que
Les modules OPV de Dracula Technologies trouvent naturellement des débouchés dans les objets de notre quotidien qui fonctionnent à piles, comme les télécommandes et les détecteurs de fumées. Avec un rendement de 61 à 72 µW pour 100 lux (un éclairage général intérieur faible), les dispositifs sont à même de remplacer les piles. Un marché d’autant plus accessible que l’entreprise développe un dispositif de stockage sur film flexible via une technologie en couche directement intégrée sur le module par impression jet d’encre. Baptisée LAYER®Vault la technologie permet de fournir de l’énergie à un appareil même lorsque celui n’a pas été exposé à la lumière (noir complet) pendant une courte durée – quelques heures, une nuit.
Aujourd’hui Dracula a signé un premier contrat avec la société COOLR sur des applications de caméras autonomes pour la gestion des stocks dans les frigos. « Nous parlons de plusieurs de centaines de milliers de pièces par an dans les prochaines années », précise Brice Cruchon.
D’autres applications sont envisagées pour le marché des étiquettes de prix digitales de la grande distribution, pour les étiquettes de suivis logistiques intégrés aux produits pour la gestion des stocks par exemple, les dispositifs de géolocalisation du bétail ou encore dans les cartes/puces intelligentes (métro, cartes d’identité, …) qui pourraient devenir réceptives et non plus seulement émettrices.
L’inauguration de la «Green Micro Power Factory» a réuni plusieurs clients potentiels. Des intérêts ont été formulés dans d’autres branches mais il est trop tôt pour en parler. Dracula Technologies compte aujourd’hui 40 collaboratrices et collaborateurs. D’ici 2026, elle entend atteindre un chiffre d’affaires de 40 millions d’euros et recruter une centaine de personnes, notamment des techniciens opérateurs salle blanche pour la production, des ingénieur·es process et qualité et des personnes dédiées au développement commercial.
Ce contenu est protégé par un copyright et vous ne pouvez pas le réutiliser sans permission. Si vous souhaitez collaborer avec nous et réutiliser notre contenu, merci de contacter notre équipe éditoriale à l’adresse suivante: editors@pv-magazine.com.
1 comments
En transmettant ce formulaire vous acceptez que pv magazine utilise vos données dans le but de publier votre commentaire.
Vos données personnelles seront uniquement divulguées ou transmises à des tierces parties dans une optique de filtre anti-spams ou si elles s’avèrent nécessaires à la maintenance technique du site web. Un transfert de vos données à des tierces parties pour toute autre raison ne pourra se faire que s’il est justifié par la législation relative à la protection des données, ou dans le cas où pv magazine y est légalement obligé.
Vous pouvez révoquer ce consentement à tout moment avec effet futur, auquel cas vos données personnelles seront immédiatement supprimées. Dans le cas contraire, vos données seront supprimées une fois que pv magazine aura traité votre requête ou lorsque le but du stockage des données est atteint.
Pour de plus amples informations sur la confidentialité des données, veuillez consulter notre Politique de Protection des Données.